Decades of collecting has led the museum to what we have today – a tightly packed storage area full of pieces of clothing, inconsistently labelled and hiding under aging covers. It is all tucked away in the back of the Navy Museum Collections Store.
With the recent disassembling of the museum’s Hire Collection (a disused group of Naval Uniform pieces that were previously hired out on request) a large amount of hanging storage space was freed up. Instead of simply spacing out the collection the decision was made to start a years-long project of improving the clothing storage permanently.
For the past year Collections Assistant Lori has been working hard on this project with the assistance of the rest of the Collections team, and as a fun end-of-year update we’d like to give you a window into how it’s coming along.
We began the project by dividing the hanging clothing collection into smaller bite-sized pieces. Greatcoats were our test group; first to go through a rigorous process of upgrading records, storage, and identification, and first to move to their new comfortable homes.
All garments were checked thoroughly for any signs of deteriorating conditions; mould being the biggest offender. Cramped storage leaving the clothing no room to breathe, inconsistent covering allowing mould to spread between pieces, and a lack of the infrastructure required to keep clothing in a temperature and humidity stable environment all worked together against the best efforts of the Collections staff members. Luckily, only approximately 1 in 10 garments were affected, with doeskin material being the worst offender. Any with mould blooms were frozen to kill the spores and then professionally cleaned to avoid any permanent staining.
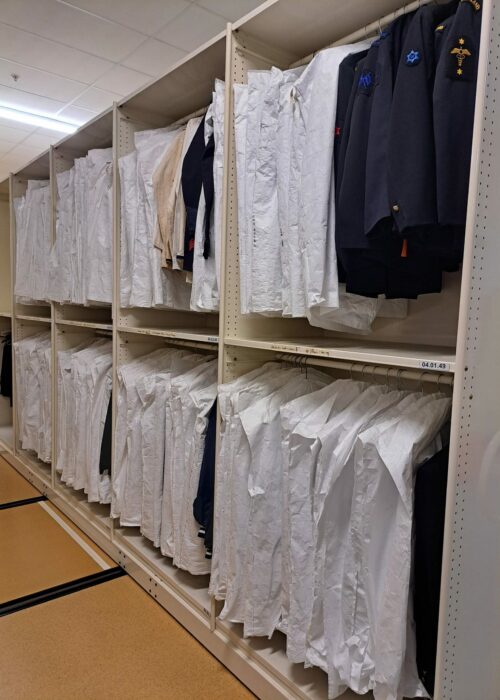
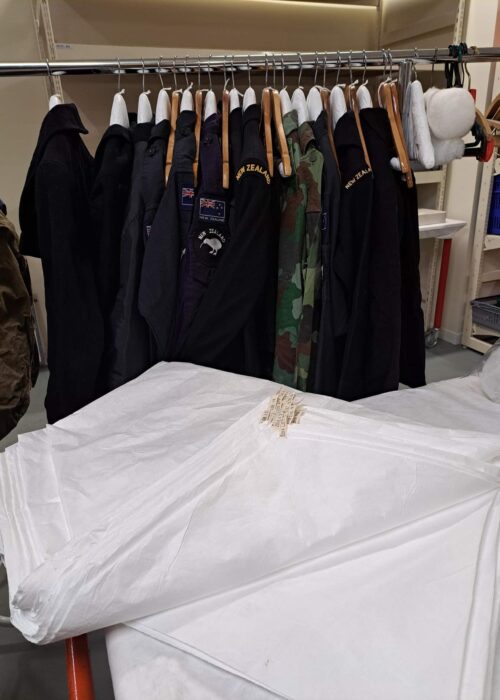
The next step was to improve their covers and labels. Bare or metal coat hangers were all replaced with custom-made padded hangers. Wooden hangers are wrapped in Dacron to cushion the hard edges and then covered in Tyvek to protect the garment from long term exposure to any harmful materials that may be present in the wood or lacquer. Many an afternoon has been spent wrapping and sewing hangers in an efficient production line!
Existing Tyvek covers that are in good condition were kept, and any uncovered garments or covers showing signs of foxing were replaced. Some covers have been made in bulk by a company in Christchurch, but those rapidly ran out and we have since made our own on the Collections Store sewing machine.
One of the most important parts of this process was permanently labelling the garments with their identifying numbers. Some have been labelled in the past, but many more have no numbering beyond an easily-displaced swing tag around the neck of the coat hanger. When numbers get disassociated from their objects it can be an extraordinary task to reunite them, and sometimes even impossible – leaving an object entirely with context and provenance. Our process for labelling clothing is to sew a small unbleached cotton label with the object’s number on it into the neck or waistband of the garment, and a matching one on the outside of the bag.
As we already have the garments out for this process, it’s the perfect time to update our digital database! We add in any data that is missing from the garment’s record and add in some high-quality images for those without.
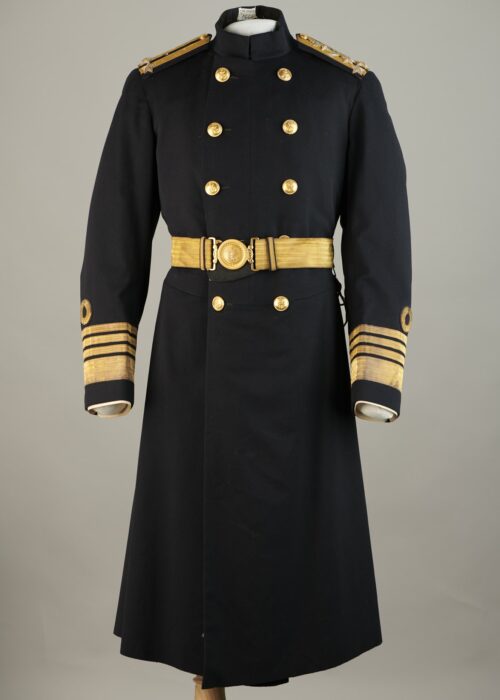
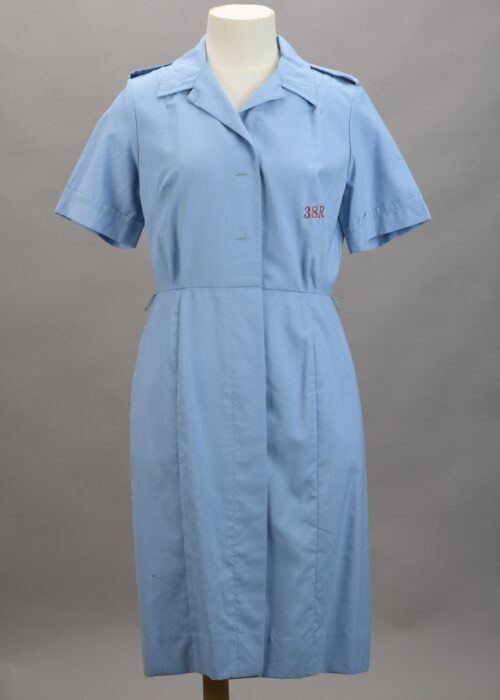
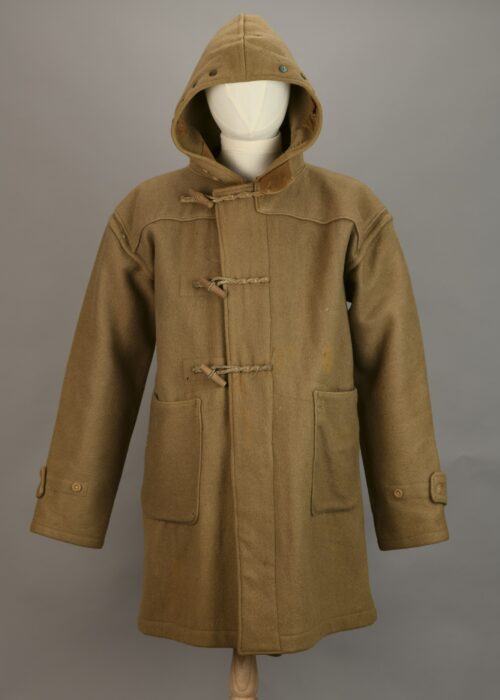
Finally the garments are placed in the new hanging clothing rack and their new location is recorded in our digital database. We have restricted numbers to 10 coats and 15 trousers per shelf, in order to prevent future overcrowding.
As of November 2024, nearly 200 hanging garments have been fully processed, with over 400 remaining. Whew!
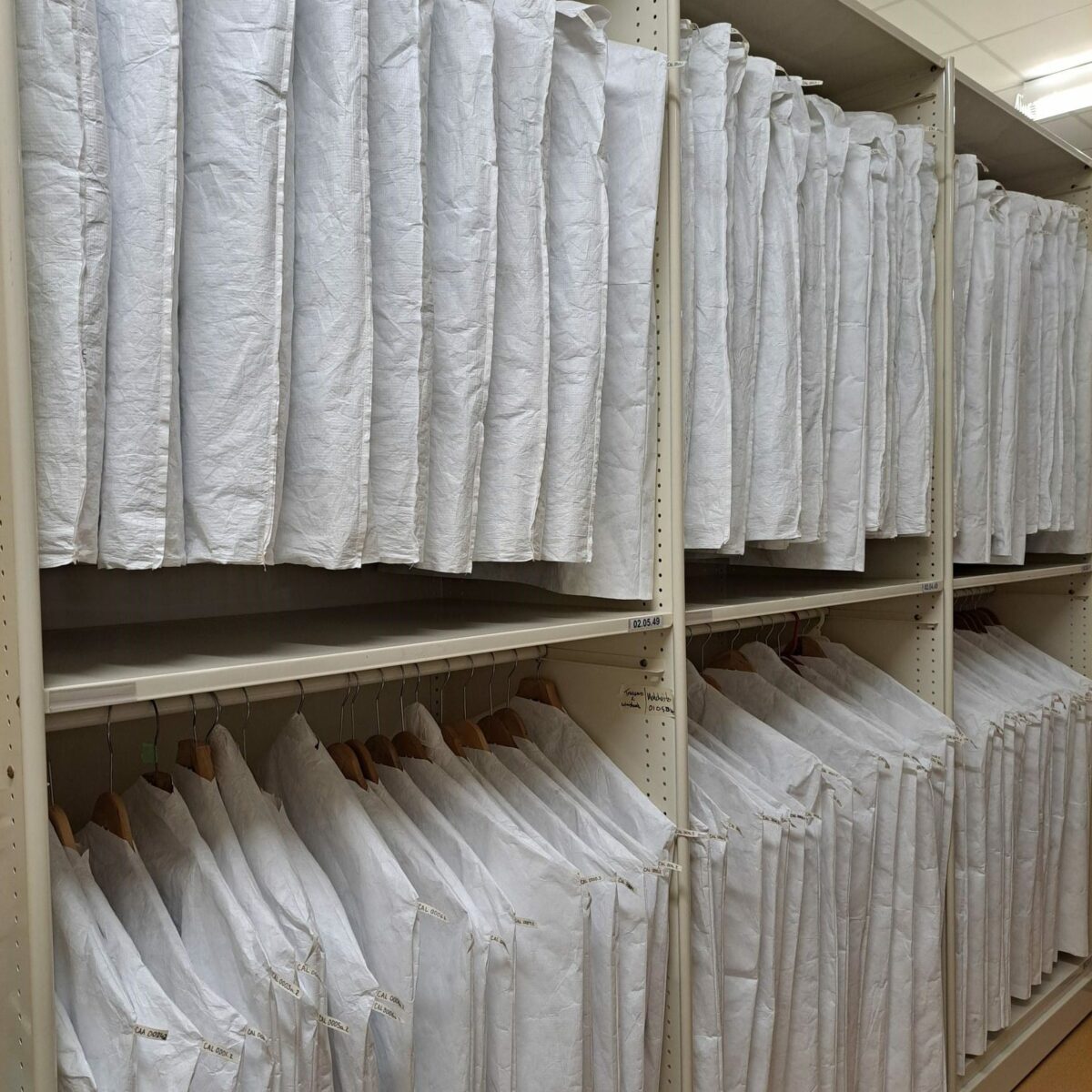